Purposes of Top Spray Granulation
Top spray granulation is most commonly used to improve the flow characteristics of powder. Other advantages include increasing particle size, density, and surface area as well as reducing dust emissions.
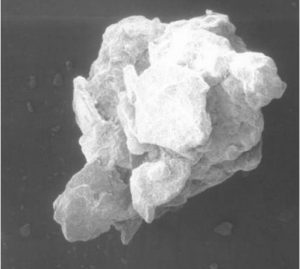
Top spray granulation is most commonly used to improve the flow characteristics of powder. Other advantages include increasing particle size, density, and surface area as well as reducing dust emissions.
An atomizing spray gun with tri-axial wand is the standard spray gun used with a FLO-COATER® system. Solution, atomization air and spray air are supplied through the spray gun assembly, creating a non-cluttered, easy to use spray gun. The number of nozzles vary depending on the batch size (up to 1,900L capacity).
The Conidur plate, standard on all FLO-COATER® systems, provides a consistent distribution of airflow across the product plate, thus improving drying efficiencies and increasing spray rates. Another advantage is that the Conidur plate provides directional airflow, assisting in the vacuum discharge of product.
With fluid bed systems, safety always must be considered as the highest priority. Due to static charge of the product, there always remains the risk of an explosive environment within the fluid bed chamber. The safety risk is heightened when solvents are used as the binding solution. FREUND designs fluid beds to an over-pressure rating of 12 bar and the explosive situation (correctly termed “deflagration”) is contained within the fluid bed chamber. FREUND also offers a vented design, which safely directs the over-pressure situation to an open, safe place.
FLO-COATER® systems can be executed in 3-piece construction. With this design, additional processing inserts can be incorporated into the system. This allows for quick-changeover of the fluid bed system from a top spray granulator to a Wurster Coater or GRANUREX® rotor processor.