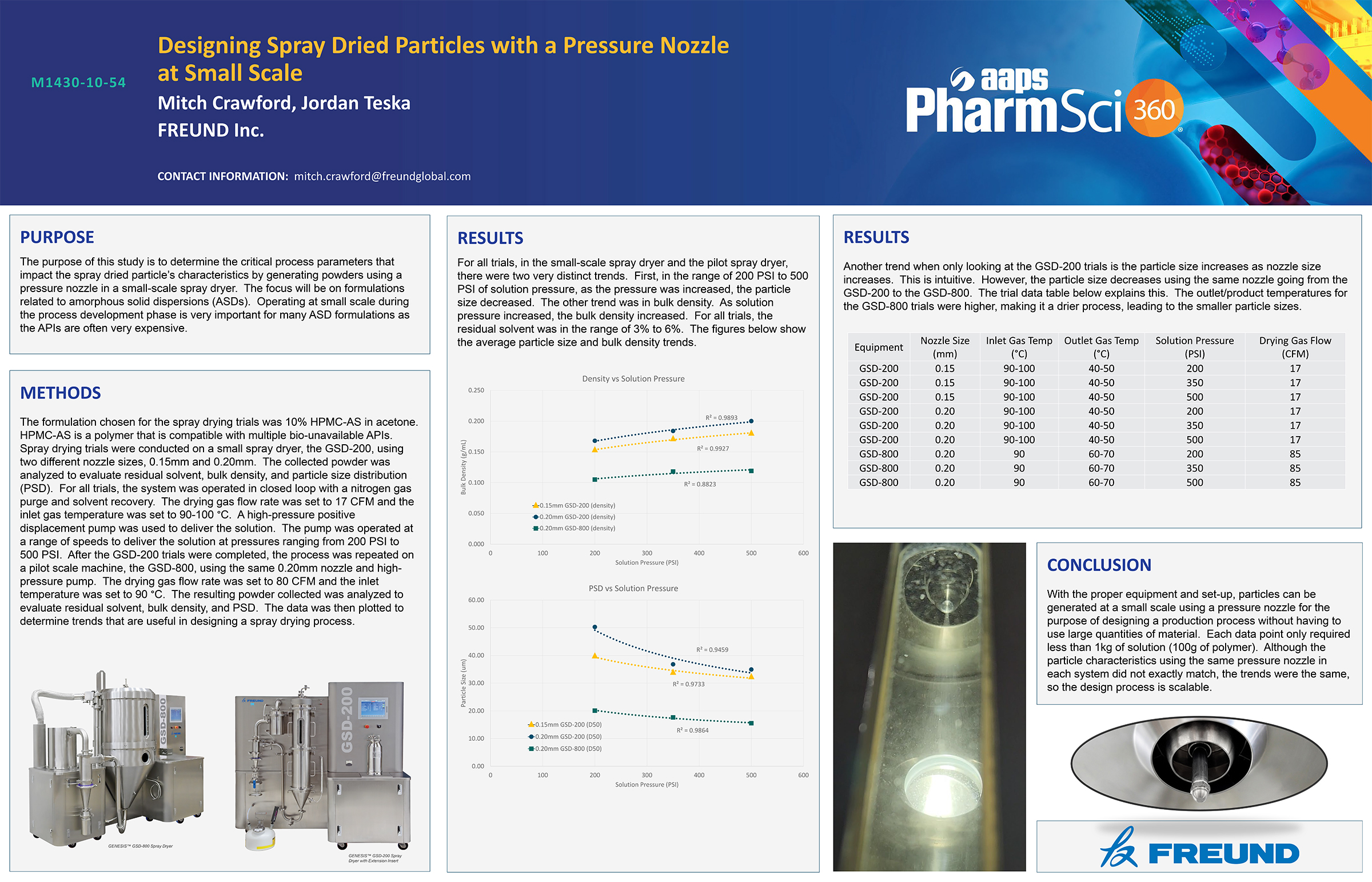
Designing Spray Dried Particles with a Pressure Nozzle at Small Scale
The purpose of this study is to determine the critical process parameters that impact the spray dried particle’s characteristics by generating powders using a pressure nozzle in a small-scale spray dryer. The focus will be on formulations related to amorphous solid dispersions (ASDs). Operating at small scale during the process development phase is very important for many ASD formulations as the APIs are often very expensive.