The GRANUMEIST® (GMX) High Shear Granulator Mixer systems have been used for decades in the pharmaceutical industry. They are designed for efficient and homogeneous wet granulation of powders to form medium to high density granules with excellent flowability and compressibility characteristics. A high-shear mixer can be used to create emulsions, suspensions, lyosols (gas dispersed in liquid), and granular products. These mixers play an important role in many industries including adhesives, chemical, cosmetic, food, pharmaceutical, and plastics industries for emulsification, homogenization, particle size reduction, and dispersion.
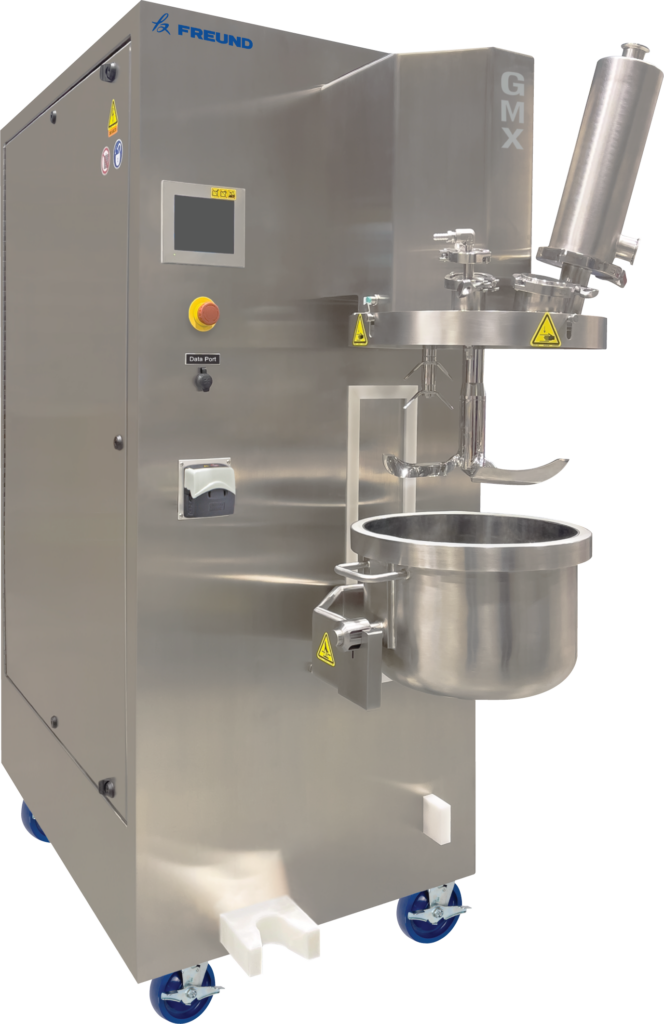
Whether you are a rookie or a skilled professional in the material processing industry, this can be an important guide to use when searching for a high shear granulator.
Applications for High Shear Mixer Granulators
The main purpose of using high shear mixers is for mixing, granulating, humidifying, homogenizing, and serving pharmaceutical materials. Furthermore, you can use this equipment to mix both dry and wet powders.
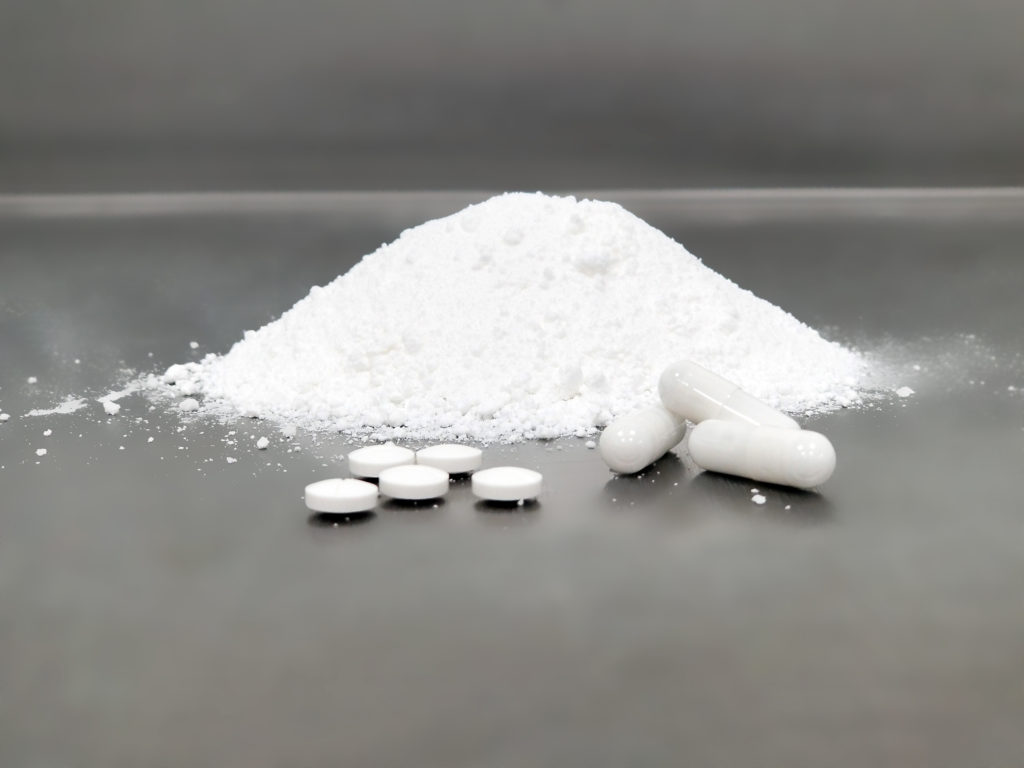
Main Parts of The High Shear Granulation Machine
The number of parts and designs can differ depending on the type of machine. It is important to evaluate these parts to be sure that the machine will meet the various performance specifications and requirements.
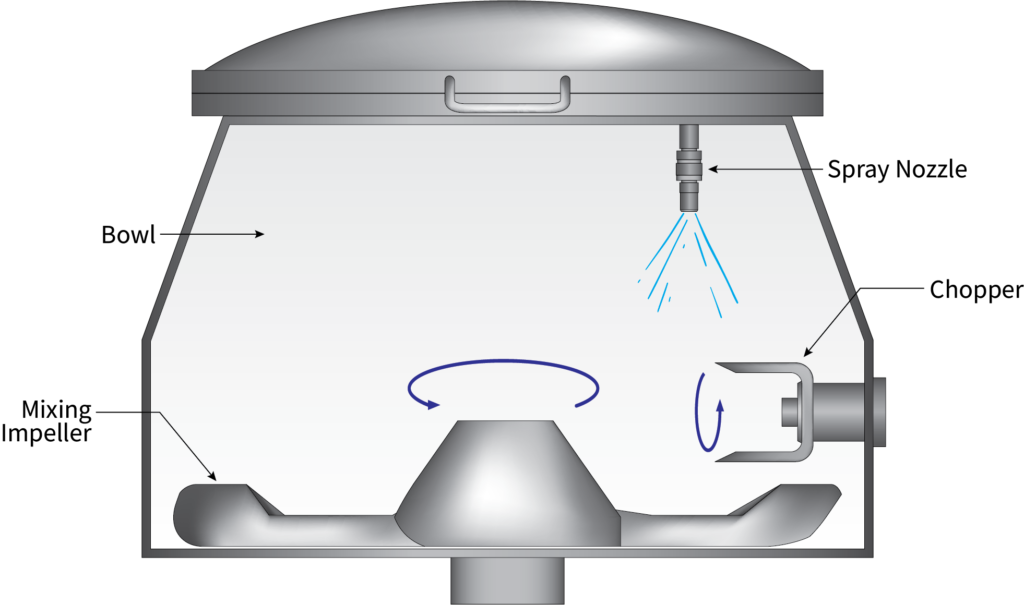
Here are key parts of this powder granulation equipment:
- Mixing Impeller
- Cylindrical Mixing Bowl
- Chopper
- Discharge Port
- Motor to Drive the Impeller
- Spray Nozzle for Binding Liquid
- Compressed Air
- Control System
Generally, these are the basic parts of the granulation machine. The precise design and coupling mechanism ensure uniform and high-quality granules.
Types of High Shear Mixer Granulators: Lab Scale to Production!
We offer two styles of GRANUMEIST® granulators, GMX Top-Drive systems where the mixer and chopper enter through the top/lid and GMXB Bottom-Drive systems with the mixer and chopper enter through the bottom and side of the product bowl. Both series of mixers can work with aqueous and solvent processing along with 12-Bar pressure explosion proof configuration.
Evaluating the design must include all parts such as (not limited to these):
- Granulation Container
- Impeller Design
- Chopper Design
- Sealing Mechanism
- Drive Mechanism
- Granules Discharge
- Machine Frame and Structure
- Granules Milling
- Spraying Nozzle
- Electrical and Control Panel
At any point, the high shear granulator should have an ergonomic design that optimizes performance.
Let me give you an example:
Structure and Frame of the Freund-Vector GMX(B) High Shear Granulator Mixer
- We only use high quality 316 SS for all parts and parts that are in contact with the product.
- This is an important criterion as part of the cGMP compliance.
High Shear Granulator Impeller and Chopper Design
- Should you go for a three-blade or a two-blade impeller design?
- Three-blade impellers will require high rotational speeds that can result in thermal stressing, though, it will produce dense granules.
- Two-blade impeller that has elongated side wings ensure rapid mixing at low rotational speeds.
- Other aspects here may include position and rotating speed of both the chopper and impeller.
In short, the design of every component and part of high shear mixer granulator will affect performance, efficiency, safety, and reliability of the machine.
Consider Degree of Accuracy
You need to be precise when it comes to this. Remember, in pharmaceutical material processing, accuracy is a crucial characteristic.
First, the design should guarantee uniform granulation. If possible, the granules should be round and strong.
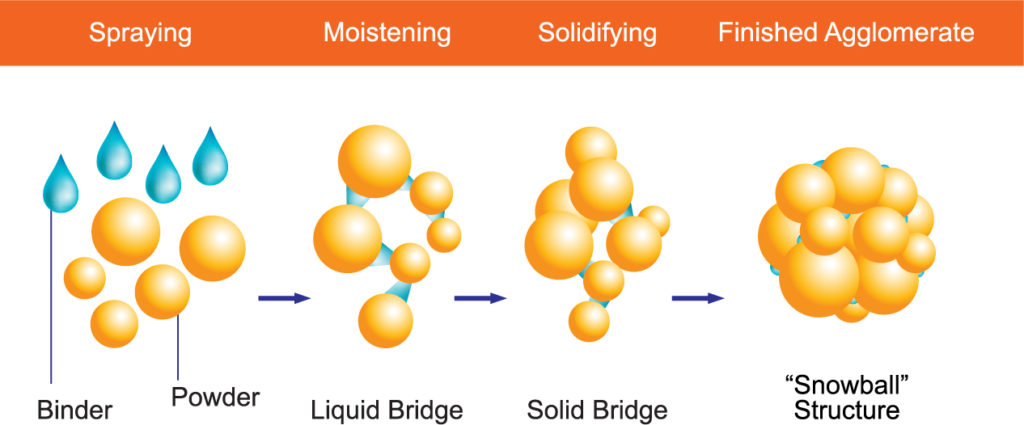
Second, the cylindrical mixing bowl should process a wide range of batch sizes. This will save you the cost of buying a new equipment or the time-consuming process of changing parts. Freund-Vector offers a wide range of batch capacities from 1L up to 2000L’s.
Regulatory Requirements
There should be proof that the equipment adheres to a strict quality manufacturing process. The cGMP is a crucial compliance requirement for all pharmaceutical equipment. The cGMP regulations require that every machine should have tight seals. Freund-Vector uses non-inflatable seals that are superior for easy removal and cleaning, puncture resistant and supports consistent operation.
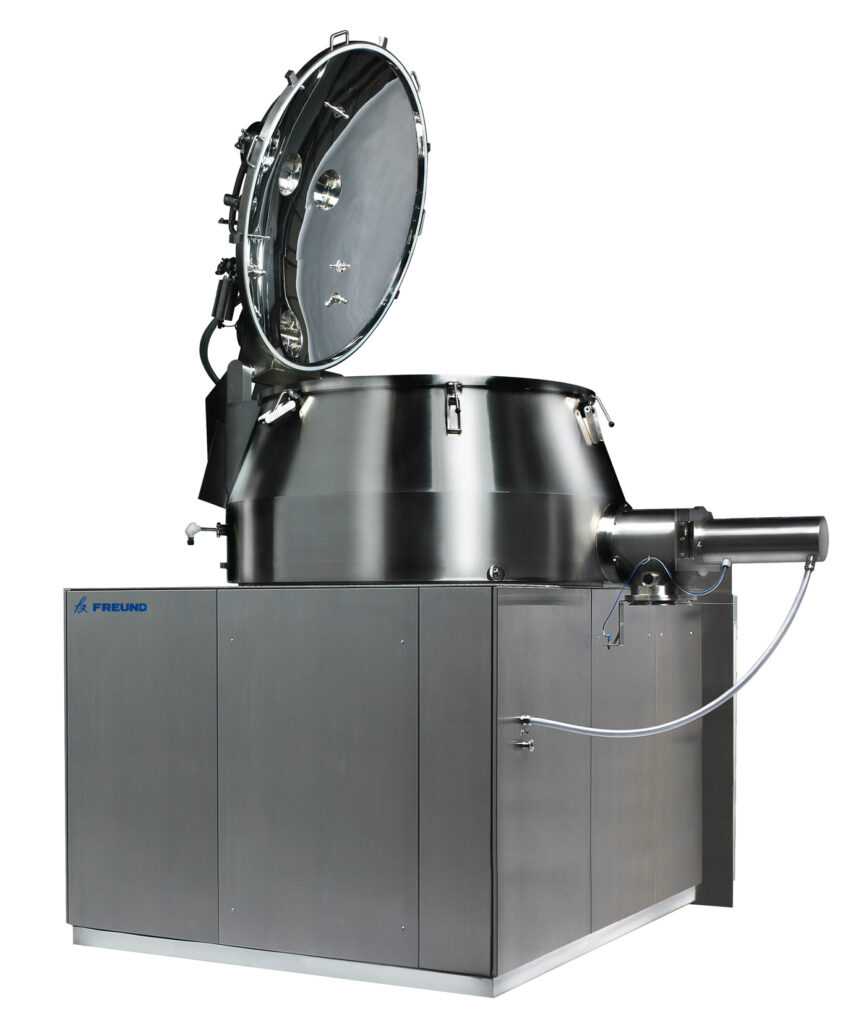
This describes why the entire structure of high shear mixer granulator is made from stainless steel. The equipment should be made from FDA approved material.
The Working Principle of High Shear Mixer Granulator
After switching on the granulator, the next steps go as follows:
- Dry Blending/Mixing the Powder
- Binder Addition (Granulation Liquid)
- Powder then Becomes Wet
- Powder Granules Begin to Form
- Powder Densifies
- Attrition and breakage of Granules
Controls that Granulation Machine Use
High shear granulators feature a wide range of technologies. All these aims to ensure efficiency and the overall reliability of the machine.
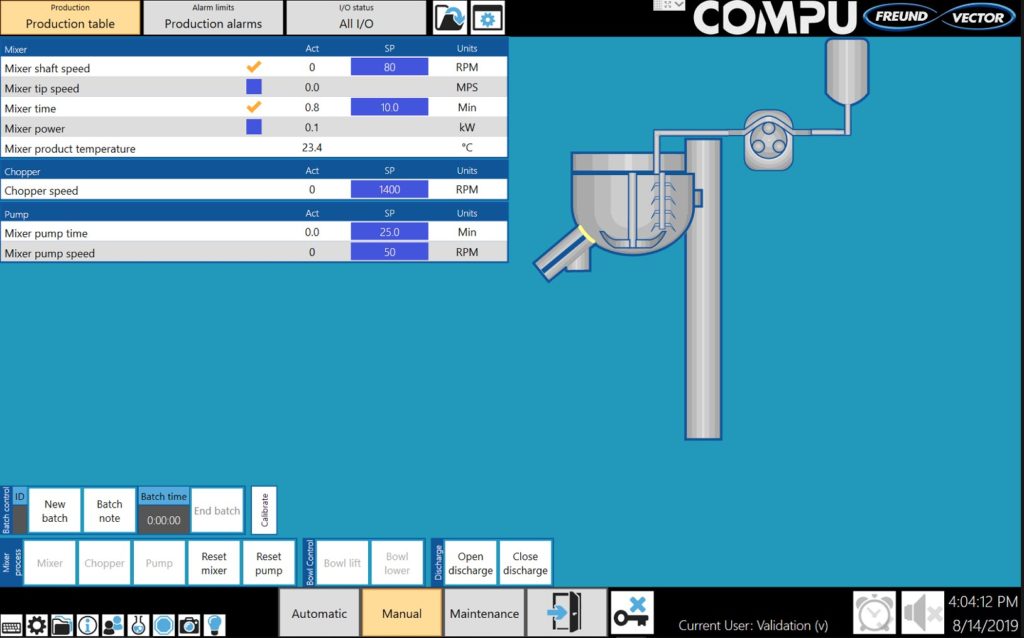
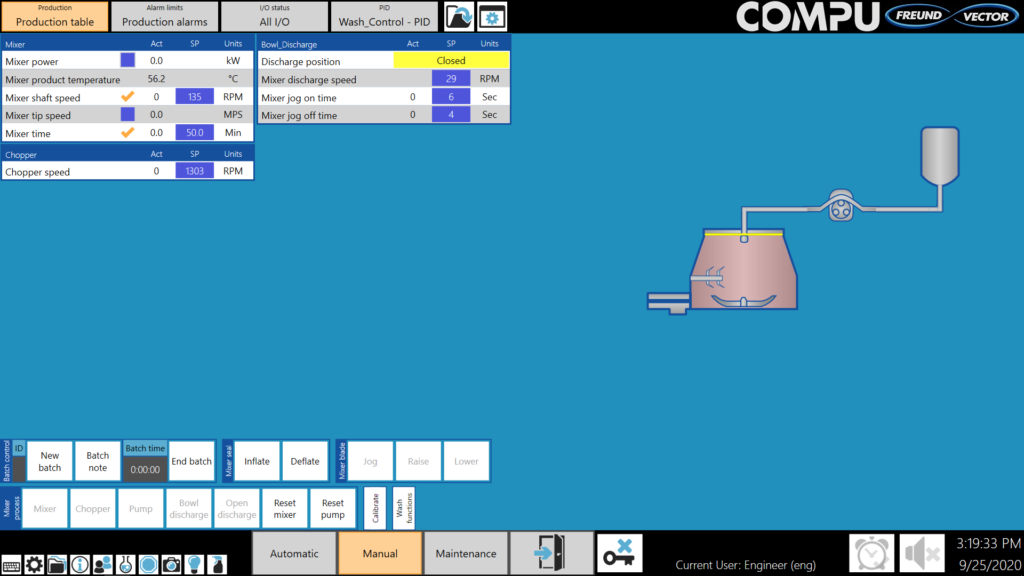
For instance, a high shear granulator may feature a fully automatic system. Freund-Vectors Color Touch Screen Control System and upgradable COMPU system are a perfect choice for most applications.
Here are some features.
- Validatable Control System
- Automatic (Recipe-Driven) and Manual Modes
- Data Collection Port
- Multiple End-Point Detection Parameters
- Mixer Power
- Calculated Mixer Torque
- Granulation Time
- Product Temperature
- Solution Delivery
- COMPU Control System (Optional)
- 21 CFR Part 11 Data Recipe Handling System
- Designed for Granulation Suites
- And Much More
Which Factors Affect the Quality of Powder Granulation?
Choosing a good powder granulation machine is not enough. There is a wide range of factors that may influence the formation of the final granules either directly or indirectly. These include:
- Physical and Chemical Properties of the Powder
- Material Loading
- Types and Quantity of Binder Solution
- Applying Granulation Solution (Method and Rate).
- Impeller Speed and Chopper Speed
- Design of Granulator Machine
Advantages of Powder Granulation Machine
There are several reasons why this machine is popular most pharmaceutical processing industry. Some of the key advantages include:
- A Fast Powder Granulation Process
- Precise and Accurate Granule Production
- Requires a Small Quantity of Binder Solution
- Short Powder Drying Time
- A Predictable Production Process
- Greater Densification and production of less friable granules
- Easy Scale-Up
Conclusion
So, High Shear Mixers | Is It Right For You? Contact us today and let’s find out why our high shear mixers are a great choice for granulation equipment. It is a fast and reliable process that plays an important role in agglomeration of powder particles either for further processing or as a final product.